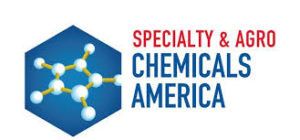
RT Process to Exhibit at Chemicals America
July 18, 2016Transferring chemical processes to toll manufacturers

The process of moving a chemical process from one facility to another can be full of challenges and pitfalls. In some cases the process owner is able to locate identical equipment as the original manufacturing process; this is the best case condition assuming that the support infrastructure will allow the equipment to operate at the same process parameters as in the original installation. Even with identical equipment however, slight changes due to support systems can at times be seen even with a direct transfer. The use of steam versus hot oil, water quality and supply rates, agitation, air or nitrogen pressure are a few factors which can causes differences from one facility to another even with the same equipment.
In other cases when identical equipment is not available, process owners must break down their process into fundamental unit operations (mixing, drying, reaction equilibrium and kinetics) and work to assign process variables to each unit step. This fundamental approach lays the foundation for an understating of the process and also provides for success criteria in the transfer of a process from one location to another. Ultimately, the true test of success is product performance, however a well thought out set or key process variables will greatly increase the odds of successful performance on the first attempt.
At RT Process, we will help you develop the program to assess successful transfer of your process and the development of process parameters to insure processing steps which mirror the original process. We seek to understand the customer’s process to the extent that the technical team can scan a set of well thought-out key process variables and be assured that the output of the process at RT will be of identical quality as their own manufacturing operation.